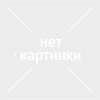
Продавец оборудования для бизнеса
Floria (частное лицо)

Телефон
договорная цена
г. Другие страны
Обзор
Система обнаружения шлака в инфракрасном конвертере использует тепловизор дальнего инфракрасного диапазона для мониторинга ситуации при выпуске конвертера в режиме реального времени и подключается к главному управляющему компьютеру в электрощитовой посредством преобразования и передачи видеосигналов. Интенсивность излучения в диапазоне длин волн инфракрасного излучения 7-14 мкм различна для различения расплавленной стали и шлака. На более поздней стадии выпуска конвертера жидкая сталь постепенно уменьшается, а сталеплавильный шлак вовлекается в расплавленную сталь и вытекает из выпускного отверстия. После того, как тепловизор распознает сталеплавильный шлак при измерении температуры изображения, он подаст сигнал тревоги в соответствии с пороговым значением содержания шлака, установленным программным обеспечением. Тепловизор запустит скользящую пластину, чтобы закрыть выпускное отверстие, чтобы реализовать контроль шлака в выпуске конвертера и обеспечить максимальный выход расплавленной стали и минимальный контроль содержания сталеплавильного шлака.
Эффект обнаружения шлака при выпуске конвертера имеет большое значение для контроля количества шлака. Разработанная нашей компанией система обнаружения и контроля конвертерного шлака осуществляет бесконтактный контроль потока выпускаемой стали через детектор-тепловизор дальнего инфракрасного диапазона. Он может определять состояние шлака в режиме реального времени и выдавать сигнал тревоги и систему управления, которая может заменить ручной визуальный осмотр и обеспечить точный, эффективный и стабильный эффект обнаружения шлака. Когда система обнаруживает шлак, интеллектуальный блок управления быстро принимает решение о подъеме печи и блокировке шлака и выдает сигнал тревоги.
Как показано на рисунке 1, система включает в себя тепловизор, передний блок защиты от продувки, передний электрический шкаф, шкаф распределения электроэнергии, главный монитор управления, монитор камеры качающейся печи, звуковую и световую сигнализацию, программную систему мониторинга шлака инфракрасного преобразователя и т. д.
Особенности тепловизора
1. Диапазон измерения температуры составляет 200–2000 °C, высокая точность измерения температуры и возможность установки нескольких интервалов измерения температуры.
2. Система тепловидения высокого разрешения, изображение четкое, а цвет изображения можно свободно маркировать в соответствии с установленной температурой.
3. Благодаря функции сигнализации горячей зоны зона сигнализации и диапазон температур могут быть установлены произвольно.
4. С функцией отслеживания горячей зоны.
5. Оснащен специальным инфракрасным фильтром 7 ~ 14 мкм.
Технические параметры
1. Диапазон измерения температуры: 200°C ~ 2000°C.
2. Точность измерения температуры: 2%
3. Точность обнаружения и точность сигнализации: ≥98%
4. Разрешение: ≥ 0,5 ℃
5. Пиксели: 640x240PT.
6. Диапазон: 7 ~ 14 мкм
7. Поле зрения: 7,5°×5,5°.
8. Частота кадров: ≥ 25 кадров/сек.
9. Срок службы оборудования: ≥5 лет.
10. Нормальная скорость работы системы автоматического управления: ≥99%.
Система обнаружения шлака в инфракрасном конвертере использует тепловизор дальнего инфракрасного диапазона для мониторинга ситуации при выпуске конвертера в режиме реального времени и подключается к главному управляющему компьютеру в электрощитовой посредством преобразования и передачи видеосигналов. Интенсивность излучения в диапазоне длин волн инфракрасного излучения 7-14 мкм различна для различения расплавленной стали и шлака. На более поздней стадии выпуска конвертера жидкая сталь постепенно уменьшается, а сталеплавильный шлак вовлекается в расплавленную сталь и вытекает из выпускного отверстия. После того, как тепловизор распознает сталеплавильный шлак при измерении температуры изображения, он подаст сигнал тревоги в соответствии с пороговым значением содержания шлака, установленным программным обеспечением. Тепловизор запустит скользящую пластину, чтобы закрыть выпускное отверстие, чтобы реализовать контроль шлака в выпуске конвертера и обеспечить максимальный выход расплавленной стали и минимальный контроль содержания сталеплавильного шлака.
Эффект обнаружения шлака при выпуске конвертера имеет большое значение для контроля количества шлака. Разработанная нашей компанией система обнаружения и контроля конвертерного шлака осуществляет бесконтактный контроль потока выпускаемой стали через детектор-тепловизор дальнего инфракрасного диапазона. Он может определять состояние шлака в режиме реального времени и выдавать сигнал тревоги и систему управления, которая может заменить ручной визуальный осмотр и обеспечить точный, эффективный и стабильный эффект обнаружения шлака. Когда система обнаруживает шлак, интеллектуальный блок управления быстро принимает решение о подъеме печи и блокировке шлака и выдает сигнал тревоги.
Как показано на рисунке 1, система включает в себя тепловизор, передний блок защиты от продувки, передний электрический шкаф, шкаф распределения электроэнергии, главный монитор управления, монитор камеры качающейся печи, звуковую и световую сигнализацию, программную систему мониторинга шлака инфракрасного преобразователя и т. д.
Особенности тепловизора
1. Диапазон измерения температуры составляет 200–2000 °C, высокая точность измерения температуры и возможность установки нескольких интервалов измерения температуры.
2. Система тепловидения высокого разрешения, изображение четкое, а цвет изображения можно свободно маркировать в соответствии с установленной температурой.
3. Благодаря функции сигнализации горячей зоны зона сигнализации и диапазон температур могут быть установлены произвольно.
4. С функцией отслеживания горячей зоны.
5. Оснащен специальным инфракрасным фильтром 7 ~ 14 мкм.
Технические параметры
1. Диапазон измерения температуры: 200°C ~ 2000°C.
2. Точность измерения температуры: 2%
3. Точность обнаружения и точность сигнализации: ≥98%
4. Разрешение: ≥ 0,5 ℃
5. Пиксели: 640x240PT.
6. Диапазон: 7 ~ 14 мкм
7. Поле зрения: 7,5°×5,5°.
8. Частота кадров: ≥ 25 кадров/сек.
9. Срок службы оборудования: ≥5 лет.
10. Нормальная скорость работы системы автоматического управления: ≥99%.